When it comes to training operators for welding automation, the message from our LinkedIn audience was clear: hands-on experience is king.
In a recent poll, 46% of respondents ranked hands-on training as the most critical factor in preparing operators for automation success. Welding knowledge followed closely—another key component that can’t be overlooked.
It’s a strong signal from the field: operators don’t just need theory—they need to do the work. They need to move robots, strike arcs, troubleshoot live scenarios, and understand not just what the system can do, but how it works on the shop floor.
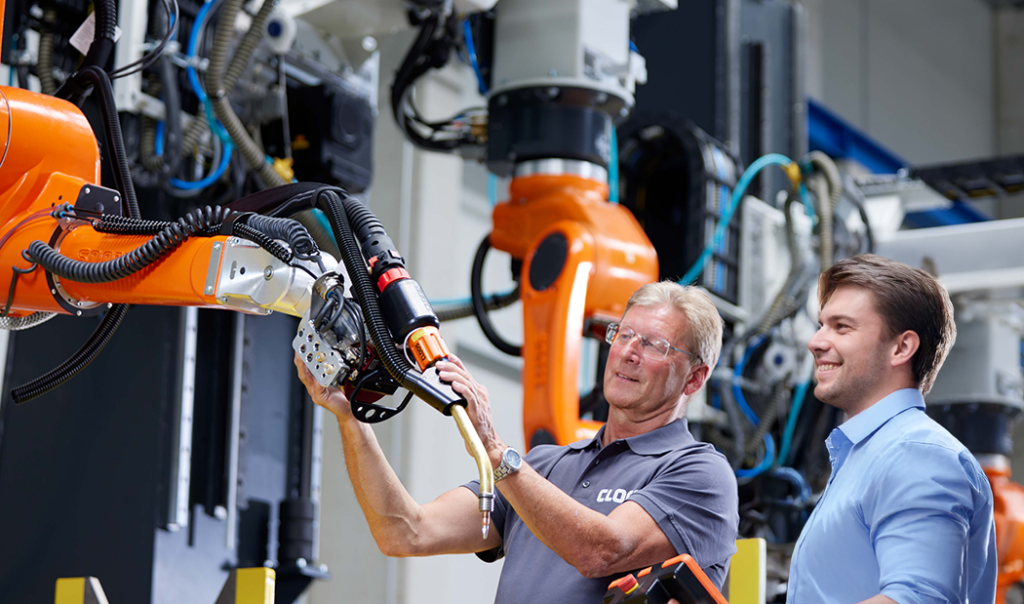
Why Hands-On Matters
Welding automation is as much muscle memory as it is mindset. You can’t teach someone how to ride a bike by handing them a manual—and the same goes for teaching someone to program or operate a robotic welder.
When evaluating a vendor or partner for welding automation, consider asking:
- What does your training program look like—classroom, simulation, live arc, or all of the above?
- Can you train both seasoned welders and new operators?
- How do you tailor training to real-world production goals?
- What support is available post-installation?
These questions go beyond curriculum—they speak to the partner’s philosophy around education and adoption. It’s not just about delivery; it’s about mentorship and transformation.
The Role of Welding Knowledge
While hands-on practice builds confidence, welding knowledge builds competence. Understanding torch angles, wire feed speeds, heat inputs, and metallurgy—this is where automation becomes welding automation, not just button pushing.
That’s where CLOOS takes a different path. We don’t train operators to be button-pushers. We train them to be robotic welders—with the insight to adjust and the confidence to lead. Our roots are in welding, and we’ve built automation on that foundation. That’s why our training combines practical application with welding wisdom from day one.
A Straight-Talk Takeaway
You don’t need a partner that just drops off a machine and walks away. You need one that sticks around, teaches, troubleshoots, and helps your team grow into the technology.
Anyone can deliver a robot, but few can deliver the confidence and skill to run it. That’s where CLOOS stands apart.