In today’s fast-paced manufacturing landscape, efficiency and precision are critical. Welding automation has rapidly evolved from a luxury to an industry necessity, but how did we get here, and why should manufacturers care now more than ever?
In this article, we’ll dive into the history, benefits, and key steps to adopting welding automation, with insights from Doug Zoller, President of CLOOS North America. Whether you’re just starting your automation journey or looking to optimize existing processes, this article will guide you through key considerations.
A Journey Through Welding Automation: From the 1960s to Today
Welding automation has come a long way, transforming from simple robotic arms used in the automotive industry to advanced systems powered by artificial intelligence and real-time monitoring. Here’s a quick look at the major milestones:
- 1960s: The first welding robots were introduced, primarily for spot welding in automotive manufacturing. These robots significantly improved safety and efficiency.
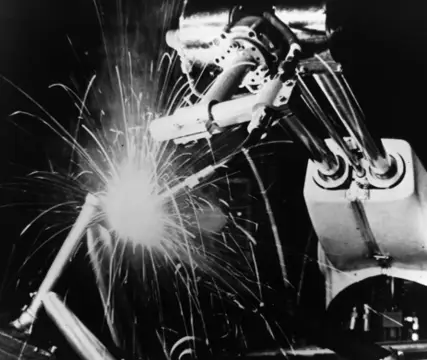
- 1970s-1980s: Gas Metal Arc Welding (GMAW) and other processes broadened the capabilities of automated systems, allowing industries beyond automotive to reap the benefits.
- 1990s-2000s: The integration of Computer Numerical Control (CNC) systems and advanced robotic welding systems made it possible to achieve unparalleled precision and consistency in complex tasks.
- 2010s-Present: Recent innovations like adaptive welding technologies and collaborative robots (cobots) have brought automation to new heights. Cobots now work side-by-side with humans, enhancing productivity and safety. Additive manufacturing and laser welding have also emerged, allowing for complex metal structures with minimal heat distortion.
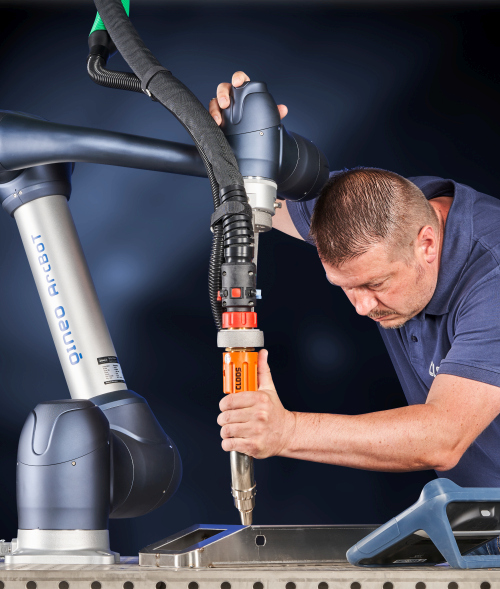
The evolution continues, and the question for manufacturers isn’t if they should automate, but how quickly they can integrate these solutions.
Why Welding Automation is No Longer Optional
With labor shortages, rising demand for quality, and the constant push for operational efficiency, welding automation is no longer a choice for manufacturers—it’s a strategic imperative. Here’s why:
1. Addressing the Skilled Labor Shortage
Automation helps offset the challenges of a shrinking skilled labor pool by allowing companies to redeploy their most experienced workers to higher-value tasks that can’t be automated.
2. Boosting Productivity
Automated welding systems can run faster and longer than human operators, drastically improving production rates without sacrificing quality.
3. Ensuring Consistent Quality
Human error is one of the biggest challenges in manual welding. Automation minimizes this by ensuring every weld meets the same high standard, every time.
4. Reducing Costs
While the initial investment in automation might be steep, it leads to significant long-term cost savings. Labor expenses decrease, and operational efficiency increases.
5. Enhancing Workplace Safety
By handling dangerous or repetitive tasks, welding robots keep workers out of harm’s way, reducing injury risks and improving overall job satisfaction.
How Welding Automation Enhances Production Efficiency
Beyond boosting productivity and quality, welding automation allows for greater efficiency through:
- Streamlined Operations: Automated systems require minimal manual intervention, keeping production lines running continuously.
- Real-Time Monitoring: Sophisticated sensors track welding parameters like temperature and arc length, allowing the system to make real-time adjustments and prevent defects.
- Faster Production Cycles: Automation enables simultaneous processes, such as welding on one station while parts are being offloaded and reloaded at another.
- Reduced Errors: Automation reduces the likelihood of defects caused by human variability, ensuring greater consistency across large production runs.
Steps to Get Started with Welding Automation
If you’re ready to explore automation for your operations, it’s essential to approach this strategically. Here are some key questions to ask:
Organizational Considerations
- What is your company’s experience with automation?
- What are your immediate business needs—do you need more capacity, better quality, or cost savings?
- Who within your organization will champion this effort? Successful automation requires strong leadership from across departments.
Technical Considerations
- What products or parts are ideal for automation? Small, simple parts? Large, complex assemblies?
- What welding codes or standards do your products need to meet, and how will automation help achieve those?
- How will you fixture your parts? This often-overlooked step is critical to achieving consistent results in automated systems.
Taking a methodical approach to these questions will ensure a smoother transition and help you avoid common pitfalls.
Building Organizational Alignment for Success
The success of any automation initiative depends on organizational alignment and communication. Forming a cross-functional team from the start, including voices from engineering, operations, and leadership, is essential to fostering accountability and inclusivity.
Additionally, introducing automation can raise concerns among employees about job security. It’s crucial to communicate openly about how automation will enhance—not replace—the workforce, positioning it as a tool to enable growth and innovation. The more transparent your company is, the smoother the adoption process will be.
Case Study: Automation in Action at KION
CLOOS recently helped KION, a global leader in industrial trucks, automate the welding of lift masts for their forklifts. By implementing advanced welding robotics, KION drastically improved production speed while maintaining the highest quality standards. This case highlights how modern automation solutions can offer both speed and precision in even the most demanding applications.
Key Takeaways for Manufacturers
- Welding automation is no longer a luxury; it’s essential to staying competitive.
- You don’t need to go big to achieve significant results—small steps toward automation can yield impressive outcomes.
- Involve the right people early in the process, and ensure your team is aligned for success.
Ready to take the next step in your welding automation journey? Connect with CLOOS North America to learn more about our cutting-edge automation solutions and how we can transform your operations.