The welding industry is evolving, but significant challenges remain as companies explore automation to enhance their operations. Recently, we conducted a LinkedIn poll to understand the biggest barriers to automating welding processes. The results highlighted two key challenges: skilled labor shortages and integrating automation with existing systems, each garnering 33% of the votes.
At CLOOS North America, we understand these hurdles and have developed solutions to help businesses overcome them while improving quality, reducing costs, and achieving greater efficiency.
Addressing the Skilled Labor Shortage
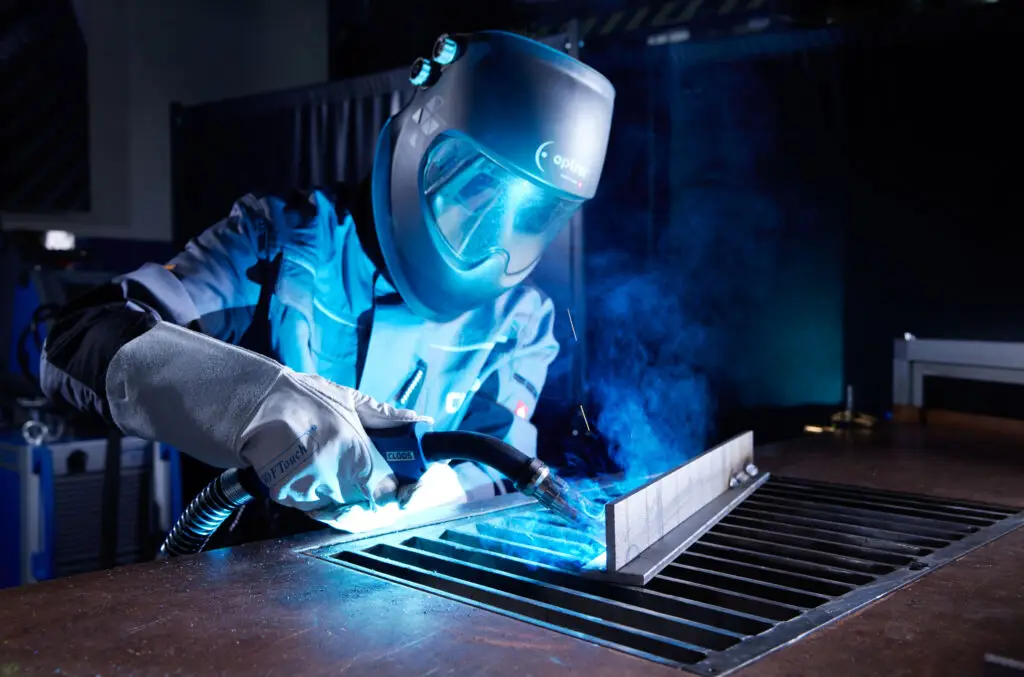
The manufacturing and fabrication sectors have long faced a shortage of skilled labor. This gap often results in operational bottlenecks, missed deadlines, and compromised quality. Welding automation provides a viable solution:
- Accessibility: Robotic welding systems are designed for intuitive operation, enabling faster onboarding of workers with minimal prior experience.
- Consistency: Automation ensures consistency in welds, thereby reducing variability that could arise from human fatigue or error.
- Scalability: With robots handling repetitive tasks, your workforce can focus on high-value activities like troubleshooting and quality assurance.
Simplifying Integration with Existing Systems
For many manufacturers, the thought of bringing new robotic systems online and incorporating them into an existing workflow seems daunting. However, modern welding automation technology is built for seamless implementation:
- Custom Solutions: Modular automation systems can adapt to your shop’s unique layout and production demands.
- Data Connectivity: Advanced systems integrate with Industry 4.0 technologies, allowing real-time monitoring and analytics for continuous improvement.
- Reduced Downtime: Comprehensive planning and support from partners like CLOOS, ensure minimal disturbances associated with the installation process.
The Broader Benefits of Welding Automation
By addressing these challenges, welding automation offers tangible benefits:
- Improved Quality: Robotic welders produce consistent, high-quality welds, reducing defects and minimizing rework.
- Cost Efficiency: Faster welding speeds and fewer errors translate into reduced material waste and lower operational costs.
- Enhanced Productivity: Automation allows for round-the-clock operation, maximizing output without increasing labor costs.
These advantages position automation as a powerful tool for navigating industry challenges and achieving long-term growth.
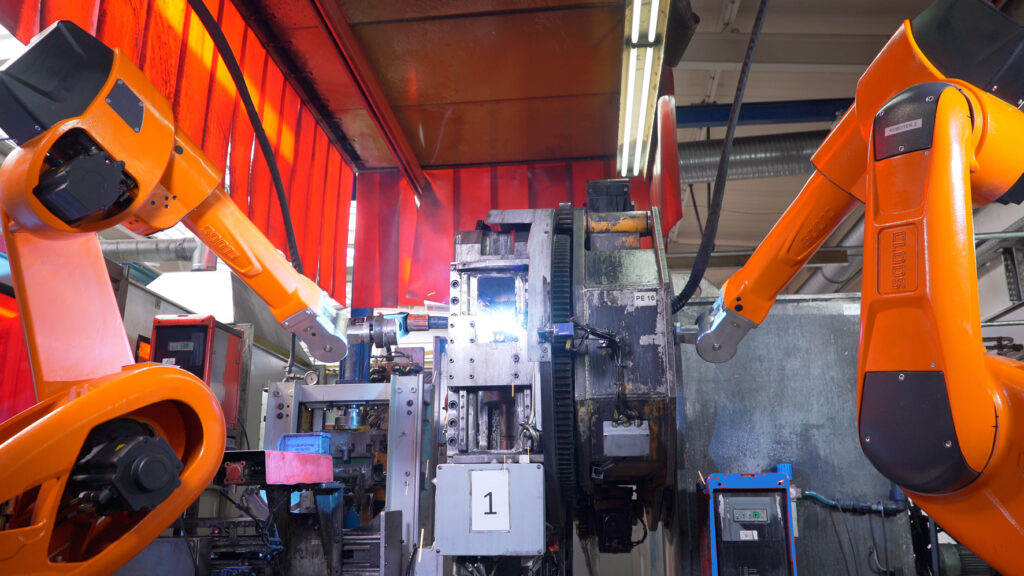
How CLOOS Can Help
With over a century of innovation in welding technology, CLOOS offers expertise and tailored solutions to help manufacturers embrace automation with confidence. Whether it’s custom integration, advanced training, or ongoing support, our goal is to empower businesses to thrive in an increasingly competitive landscape.
Are you ready to tackle the challenges of automating your welding operations?
Connect with us to learn how CLOOS can help.