In today’s fast-paced manufacturing world, automation isn’t just a luxury—it’s a necessity. But here’s the kicker: automation is only as good as the tooling behind it. Effective tooling design isn’t just about holding parts in place; it’s about driving efficiency, improving quality, and maximizing ROI. Especially when it comes to complex welding operations, where every millimeter counts.
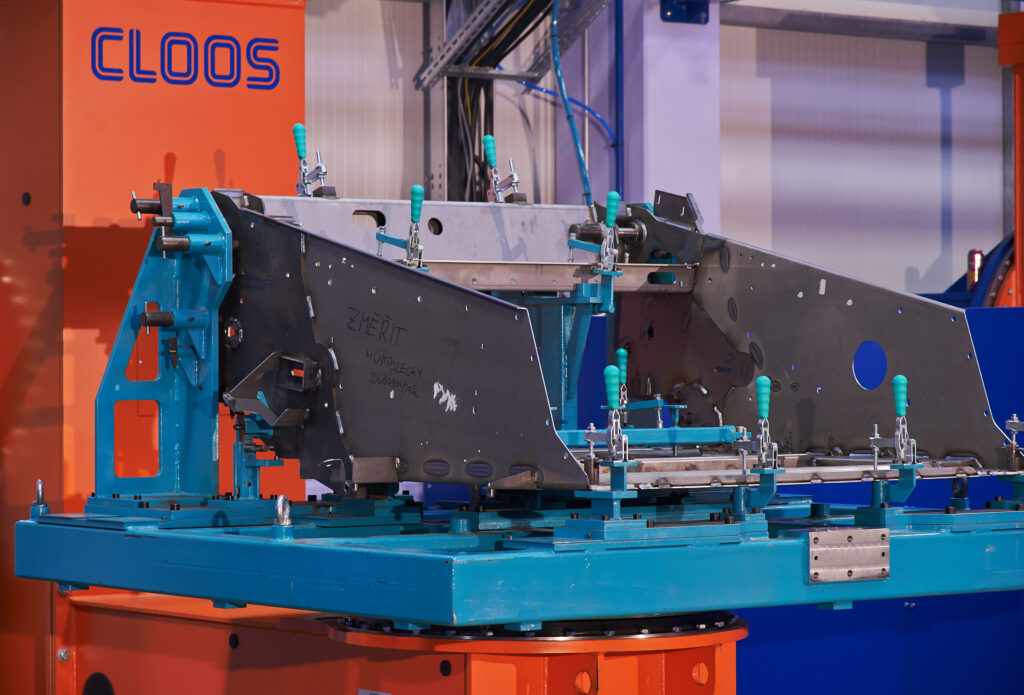
The Real Challenges of Tooling for Complex Welding Operations
Let’s not sugarcoat it—designing tooling for complex welding is tough. Industries like automotive, aerospace, and heavy machinery don’t deal with simple, cookie-cutter parts. They handle components with intricate geometries and shifting dimensions. That creates real challenges:
- Part Geometry That Keeps You Guessing: Fixed jigs and fixtures? Great for simple parts. But when you’re dealing with variable shapes and sizes, they become a bottleneck. You need adaptable solutions that can keep up without constant changeovers.
- Alignment Is Everything: Welding doesn’t forgive mistakes. Misalignment can lead to weak joints, rework, or worse—scrap. Tooling needs to lock parts in with laser-sharp precision, every single time.
- Handling the Heavy Lifting: Large, awkward parts aren’t just hard to move—they’re hard to secure. Your tooling has to do more than just hold them; it has to position them perfectly without slowing down the workflow.
- Heat Happens: Welding generates serious heat, causing materials to expand and contract. If your tooling doesn’t account for that, you’ll see distortions and alignment issues faster than you can say “rework.”
How Smart Tooling Design Changes the Game
Now, here’s the good news. When tooling is designed right, it doesn’t just solve problems—it transforms your entire operation. Here’s how:
- Workflows That Actually Flow: Great tooling reduces setup times and keeps manual interventions to a minimum. That means faster production cycles, less downtime, and higher throughput.
- Alignment You Can Trust: Advanced features like self-locating fixtures and automated clamping aren’t just nice-to-haves; they’re game-changers. They ensure parts are perfectly positioned, reducing defects and boosting quality.
- Flexibility Built In: Modular tooling systems let you pivot quickly between different part geometries. That agility is critical, especially if you’re in a high-mix, low-volume environment.
- Safety by Design: Good tooling doesn’t just protect the parts; it protects your people. Automation-centric designs reduce the need for manual handling, lowering the risk of injuries.
The Bottom Line: ROI That Speaks for Itself
Yes, investing in top-tier tooling might hit your budget upfront. But here’s why it’s worth every penny:
- Less Waste, More Wins: Precision tooling means fewer defects, less scrap, and minimal rework. That adds up fast.
- Labor Savings: Automation reduces the need for manual touchpoints, cutting labor costs and reducing the risk of human error.
- Speed to Market: Faster production cycles mean you can respond to market demands quicker, giving you a competitive edge.
- Ready to Scale: Need to ramp up production? Scalable tooling systems grow with you, no massive reinvestments required.
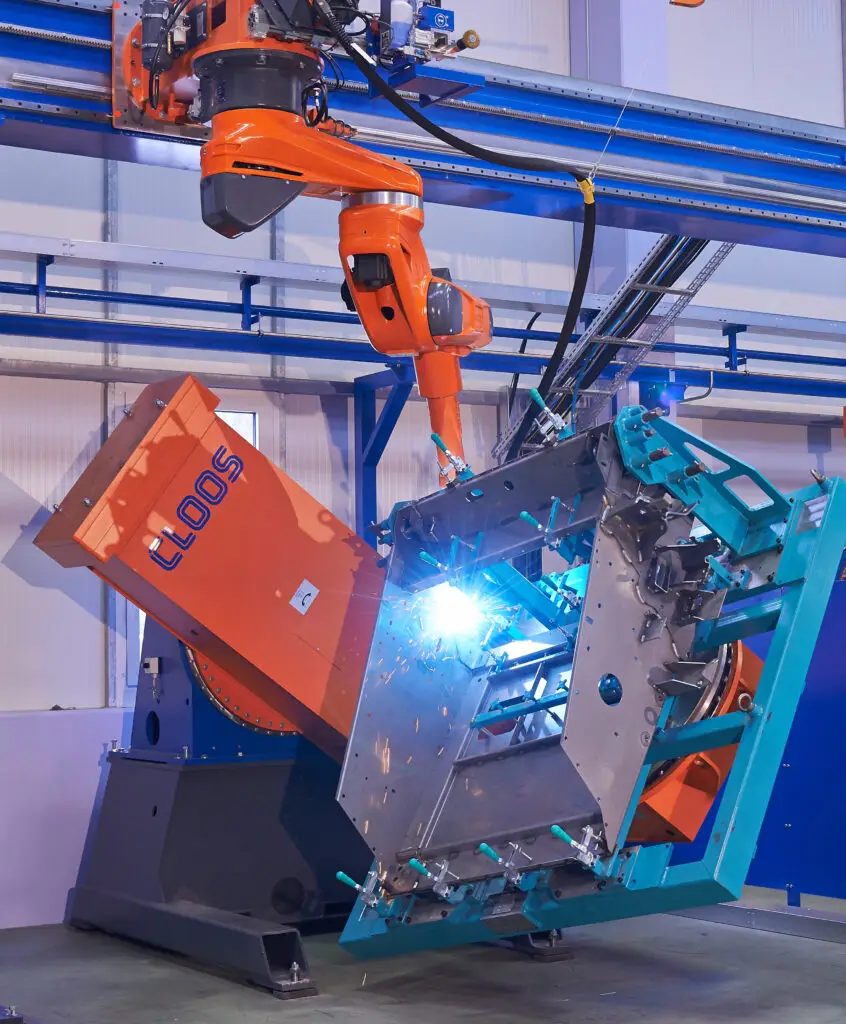
The Strategic Advantage of Smart Tooling
Smart tooling isn’t just about holding parts in place—it’s about engineering solutions that drive results. The challenges of complex welding operations are real and ever-present, but with the right approach to tooling, it’s possible to streamline workflows, enhance quality, and maximize ROI.
Automation is the future. Strategic tooling design is how you stay ahead. We’re here to help you navigate the challenges and achieve the best results. Let’s make it happen.